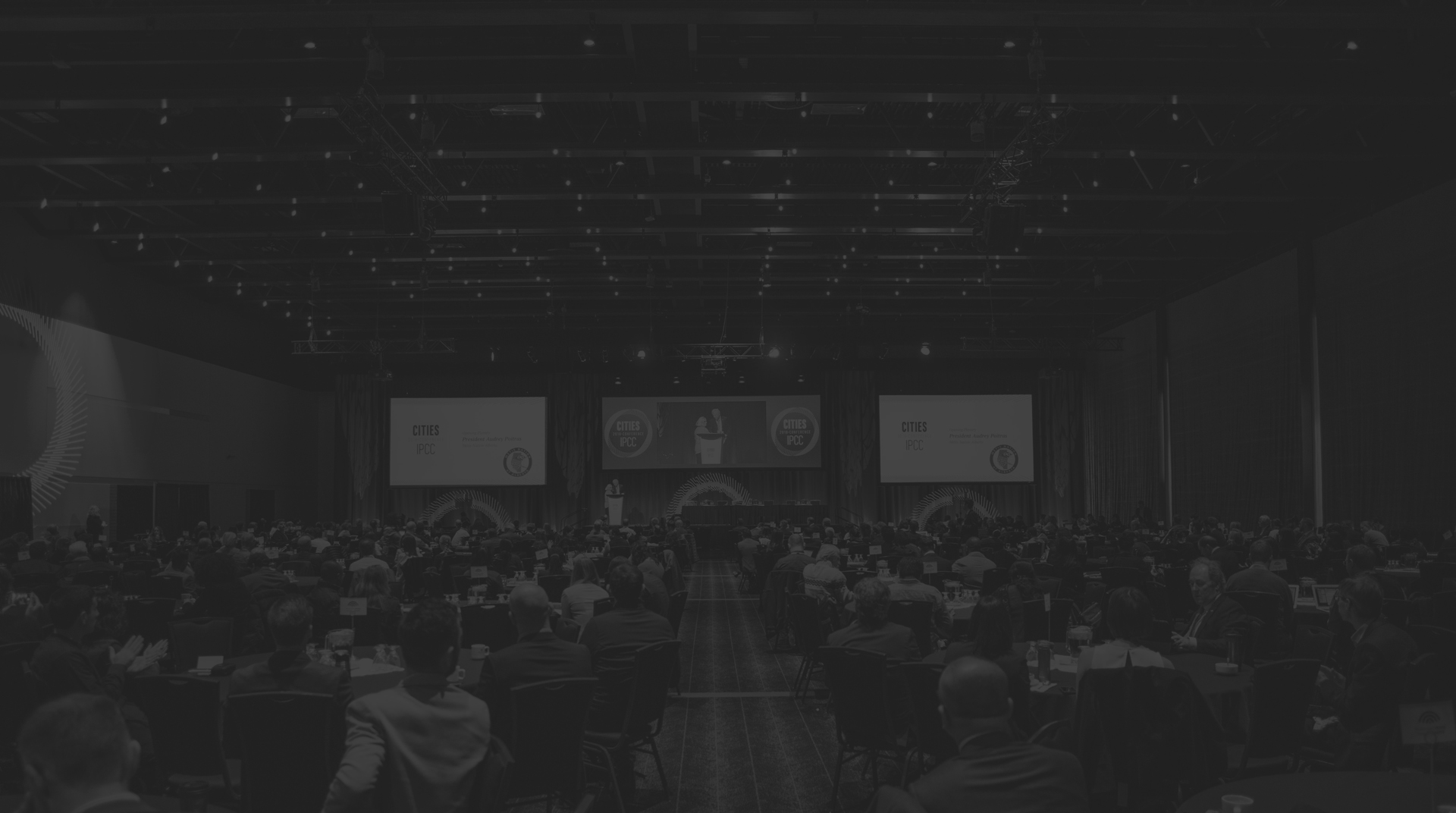
Event on: November | 18-19 | 2021
International Webinar on
Glass and Ceramics
Theme : Exploring trends that shape the future of Glass Manufacturing

Virtual Event
Glass-melting processes and therefore the effect of batch quality on these processes are considered. A Survey is performed on the basis of a heat engineering study of large capacity glass melting furnaces and mathematical modeling. Acceptable single impulse and multi-impulse deviations from an advised batch formula are estimated.
Combustion is that the burning of materials (Fuels), generally by reaction with the oxygen in air. During the reaction heat is released, and a few of the common chemical products of burning are CO2 , water vapor and soot.
Refractories are ceramic materials designed for very high temperatures encountered in modern manufacturing. More heat resistant than metals, they're used to line the hot surfaces found inside many industrial processes.
Glass Industry is using Industry 4.0 technology. It takes the glass manufacturing process to the next level, where the entire process is being controlled during a single environment process control concept. It is a common term for technologies and concepts of value chain organizations. Based upon the technological concepts of cyber-physical systems, the Internet of Things and facilitates the vision of the Smart Factory.
Glass is general produced in open-hearth furnaces during which the glass constituents are flame-heated from above to make a melt. The raw materials, sand, limestone, aragonite, dolomite, soda ash, alumina, and recycled glass are fed into the furnaces through endless or intermittent feeding system. The charge reacts and melts and subsequently exits through the feeders at the other end of the furnace
Raw Materials for Glass and Ceramics presents all classes of materials the roles they play their sources and extraction processes, and quality control issues and regulations impacting the industry. They are also used as additives to reinforce the sintering behavior of polycrystalline ceramics. Glass Batching. Glass cullet from the crushing of post-consumer glass is quickly available in urban areas. The study targeting the likelihood to use glass waste nanoparticles with an ingenious ceramic batch to supply wall and floor tiles.
The latest formed glass container will only possess a really small fraction of its theoretical strength. this means damage occurs on the surface of the glass melt in the forming process because of glass to mould contact and hot glass handling. It'd be expected that any damage inflicted on the surface of a glass article during manufacture would heal at the elevated manufacturing temperatures used, however, this doesn't appear to be true. Therefore, the true mechanism by glass strength is reduced during forming must be fully understood, and the work presented during this thesis marks this problem.
Crystalline silica may be a common mineral found within the crust . Materials like mortar, concrete, stone and sand contain crystalline silica. It is also wont to make products like glass, pottery, ceramics, bricks, and artificial stone.
The glass production process consists of highly energy-intensive. The current increase in glass demand in the world leads to industry’s energy use and Carbon emissions will continuously grow without any additional efforts for energy efficiency. There's a notable incentive to commercialize, adopt and develop energy efficiency and Carbon emissions reduction technologies for glass production.
Glass furnaces are a recycled form of glass, but difficulties in glassmaking operation were problems that make recycling unattractive in various cases. Initially, glass formulas involve not only silica but soda ash, limestone, and in several cases, coloring agents that are refined. blended and melted in precise operations.
Since furnace may be a core process of steel mills, furnace repair requires an extended repair period after blow-out.
This increases the relevance of and wish to develop new sorts of sector-based social dialogue and innovative sector- specific interventions
The hot end of glasswork is where the molten glass is manufactured into glass products. Glass structures are modeled by emulating the normal experimental melt-quench process for glass production, where a melt is gradually cooled until the system “freezes” and transforms into a glass
The raw materials that float glass is formed from are:
Batch input. Batch melting. Sand grain dissolution. Fining. Refining and conditioning. with sodium silicates or soda to make liquid sodium silicates
Quality control techniques are reviewed, including inspection oriented QC statistical process control, and design oriented QC
Glass melting requires 2 kinds of raw materials which are different types of sand and recycled glass. These raw materials are mixed together and charged in a furnace where there are melted to form molten glass. The formed molten glass has been taken out of the furnace to make its desire shape and cooled down
Refractory material or refractory is a material that is resistant to decomposition by heat, pressure, or chemical attack, and retains strength and form at high temperatures. ... Refractory materials are used in furnaces, kilns, incinerators, and reactors
Combustion technology is the process where Oxygen is used in the combustion processes for the production of glass, cement, lime, frits, ceramic pigments. These processes involve high temperatures in order to make sure high productivity and quality. Similarly, energy consumption and the environmental impact of those processes need to be contained
Methods of electrical heating include resistance heating, discharge heating, heating, and electrical phenomenon
Recovering the waste heat are often conducted through various waste heat recovery technologies to supply valuable energy sources and reduce the general energy consumption
It is rigid sort of a solid, but its molecules aren't arranged in repeating crystals. It is amorphous like a liquid. In fact, structurally there's no sharp line between a liquid and a glass
Glass formation occurs in materials of all chemical types: ionic, covalent, metallic, molecular and hydrogen bonded materials. Glasses are made up of elements, simple chemical compounds, complex organic molecules, salt mixtures and alloys
Numerical methods and simulation with comparison to experimental data for the particle uid two phase low problem involving a solid-liquid mixed
Materials Simulation and Design includes aspects of inorganic and organic materials properties, engineering systems, and applications in technology, modelling, advances in synthesis, processing, characterization, testing and design of materials and simulation of a broad range of biological materials, polymers composites, materials including ceramics, metals, glasses and semiconductors, Papers on solid materials, interfaces, and material related to microstructure surfaces and defect
The density of glass is 2.5 which provides flat glass a mass of two .5kg per m2 per mm of thickness, or 2500 kg per m3. The compressive strength of glass is extremely high 1000 N/mm2 = 1000 MPa. This means that to shatter a 1 cm cube of glass, it requires a load of some 10 tons
Electromagnetic properties of glass and amorphous materials authorize technological advancements in various fields including, but not limited to photovoltaics, fuel cells, thermoelectric, batteries, computer memory, and radiation detection. This will be focusing on a fundamental understanding of the electrical and magnetic properties of glass and glass-based composite materials
Key Optical Properties of Glass
Borosilicate glass as an immobilization material for radioactive material have reinforced the importance of scientific collaboration to get a consensus on the mechanisms manage the long period of time to dissolution rate of glass
Vitrification is currently the foremost widely used technology for the treatment of high level radioactive wastes (HLW) throughout the planet